技術資料 »
傾斜計用於追日系統
Absolute inclinometers prove advantageous in solar tracking systems
|
|
 |
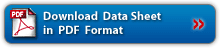
Download this document as a PDF file |
|
Misconception #1: Our systems use calculations based on the sun’s location and this formula is built into our tracker module so there is no need for an inclinometer.
The algorithm (software program) is actually needed as a part of a closed loop measuring system. But without an absolute measuring device such as an inclinometer (gravity based tilt sensing device) you really don’t know if the actual solar collector (be it module or panel) is really pointing in the right direction. The algorithm tells one where to point... the inclinometer says that yes indeed, you are actually pointing there. One can think of the algorithm as a map and the inclinometer as feet on the ground giving feedback.
There are conditions that can affect whether or not the solar collector is pointing properly and an open loop system is not able to detect this condition. The items that affect an open loop system can be corrected in a closed loop system as follows:
Seismic movement of the solar collector/foundation: A good utility scale solar generator should be designed for at least a twenty year life, however over this life, things can happen. If the system simply drives the collector X amount of steps or counts, the position is simply inferred and not known. On the other hand, an inclinometer positioned on the collector gives the system an absolute position.
Wind buffeting: Utility scale solar collectors are large devices in which prevailing winds can induce mechanical and angular offsets and if there is not an absolute sensor (aka gravity based inclinometer) indicating the true angle, then these offsets can affect the angular position. Again, an open loop system with no feedback cannot compensate for the prevailing wind condition.
Lost transmission data: Sometimes data transmission can get corrupted or lost. Having an inclinometer onboard serves (as mentioned above), as a checking standard for knowing if you are pointing where you want to be pointing.
Lost power: This condition is very similar to lost transmission data. If there is no checking standard, such as an inclinometer to give feedback, then under a lost power scenario the system must be recalibrated, thus causing lost operational time. This might be done by going back to stow position and setting off reset switches, etc. The use of an inclinometer gives the absolute angular position as soon as power is returned. No need to reset the systems, therefore eliminating the need for expensive recalibration.
Misconception #2: Our tracker system uses photodiodes and calculations based on the sun's location so if the photodiodes see no sun, then the software reprograms the tracker to find its correct position during these periods; therefore I do not need an inclinometer.
Response: Photodiodes are used to detect the sun. They are a form of an absolute sensor but they have shortcomings when it comes to placing the solar module in a stow position (which a good inclinometer based system can accomplish). When clouds occlude the sun the photodiodes supposedly fall back on the algorithm to reset, so you pay good money for a sensor that is negated when there are clouds in the sky. To further add to the concern, wind may induce an angular offset and the accompanying clouds occlude the sensor from the sun, then the system falls back on the algorithm that is negated by the wind deflecting the collector. A compounded problem that can be eliminated by the use of an inclinometer based system.
Misconception #3: We use absolute encoders and software and don't need an inclinometer. Response: An absolute encoder is similar to an inclinometer in that it doesn't lose its position in case of power outage. In loss of power/transmission the absolute encoder counts to reposition the solar module. This is a viable but costly approach. An absolute encoder with a resolution of .003 degrees is very expensive. An electrolytic dual-axis tilt sensor is available at a fraction of the cost and is by its nature a two axis product. Encoders are only one axis. A good absolute encoder may give 17 bit resolution which is dividing a 360 degree circle into 131,072 counts. Certain gravity based tilt sensors (within their measuring range) resolve easily to .05 degree which is the equivalent to 180,000 counts. All encoders have moving mechanical parts (i.e. shafts bearing, etc) that are subject to wear. Any encoder has to be shaft driven as opposed
to the inclinometer that is merely installed on the actual collector. When comparing encoders versus inclinometers, remember that an encoder is a driven device that is informing the users of positioning of a mechanical linkage that infers position.
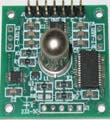
The Fredericks Company signal
conditioning board with mounted TrueTilt
metal dual-axis electrolytic tilt sensor
The Fredericks Company 0750 Series Inclinometer with RS-485 output, available with single or dual-axis tilt sensing.