Designing Products that Require Angle Measurement:
Have you Considered Electrolytic 傾斜感測器?
Article by: Andrew Ruether
Electrolytic tilt sensors have a long history of reliable operation in applications ranging from high performance avionics systems to precision seismic monitoring instruments to consumer electronics. Recent years have seen an increase in the popularity of MEMs accelerometers and tilt sensors. They can be found in consumer products such as automobiles, gaming controls, and mobile phones. Among their industrial uses are as components in construction lasers, geophysical monitoring devices, and machine levelers. Compared to electrolytic tilt sensors, MEMs generally are smaller in size and lower in cost, making them attractive components for use in manufacturing.
Given the appealing features of MEMs devices, why are electrolytic tilt sensors still in wide use?
Performance
The performance of a tilt sensor is based on several properties, including drift, repeatability, and environmental durability.
Drift presents inaccuracies in readings over time and the need for frequent re-calibrations. Most MEMs devices require stable voltage supplies, with high repeatability devices requiring control into the microvolt range. Voltage stability over time and temperature necessitates the use of expensive, high precision power supplies. Properly designed electrolytic tilt sensors have an advantage over MEMs in that their measurements are ratiometric—variations in the voltage supply do not affect the reading of the sensor and therefore do not require costly power supplies for operation.
While the performance of MEMs devices has been improving, they still cannot compete with electrolytic sensors for high-repeatability applications. High-end electrolytic products typically provide sub-arc-second repeatability; even low-cost products can now provide five arc-second repeatability[1]. The same level of performance cannot be achieved with off-the-shelf MEMs devices; one would have to use costlier, higher-end MEMs products that require expensive support electronics.
Under extreme conditions, electrolytic products also outperform MEMs devices. A product’s environmental durability greatly impacts its performance. Electrolytic devices have a proven record of performance in a wide temperature range, from -60°C to 120°C, and even wider in custom applications. They are used in industries as diverse as aerospace, construction, earth drilling, and solar tracking. With no moving parts to wear out, electrolytic devices can have long lifetimes and can handle vibration and shock. A further advantage is that they are hermetically sealed so that humidity does not pose a problem as it does for MEMs devices using plastic packages.
Simplicity
Superior performance and ruggedness aside, electrolytic tilt sensors are simple and easy to use. Integrating a tilt sensor into a system is as straightforward as reading an analog voltage—the voltage is simply proportional to the angle. Because the reading is ratiometric, a perfectly stable 5V is not required so long as the A/D reference voltage is the same as the tilt sensor drive voltage. The electronics are further simplified because the electrolytic device can operate at any voltage (5V, 3.3V, etc) and has very low power requirements. For even lower power consumption, the duty cycle can be reduced and the readings taken only when needed. Using a power source and a microcontroller with two digital ports and an A/D converter, the tilt sensor can be integrated into a system using only a few passive components.
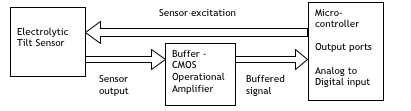
Flow chart representing signal conditioning of a single axis electrolytic tilt sensor
Furthering their simplicity and ease of use, tilt sensors come in a variety of packaging options, such as The Fredericks Company’s patented metal can electrolytic sensors. Some new ceramic sensors are designed with mounting holes to facilitate attachment into a rugged mechanical package. Like MEMs that can be mounted easily onto a circuit board, newer electrolytic tilt sensors with metal packaging manufactured by the Fredericks Company can be soldered directly onto a PCB, easily integrating with the rest of the electronics.
|
|
The Fredericks Company signal conditioning boards with mounted TrueTilt metal dual-axis electrolytic tilt sensors
|
Metal dual-axis electrolytic tilt sensors
|
For high repeatability, sensors require encapsulation to provide maximum performance over temperature, and for measurements in arc-second range angles, the sensors need to have a stable base with minimal thermal changes. In such applications, a PCB does not provide the best mounting option. There are a number of mounting solutions for encapsulation. Or, the sensor can be placed a distance away from the PCB without the need to create another custom board to mount any electronics remotely.
Support and Availability
Off-the shelf (or low cost) MEMs sensors are made for commercially-driven, high-volume applications with no promise of future availability. For applications requiring longer production cycles, purchasing managers and engineers must scramble to find replacements for obsolete parts, many times causing new board layouts or product redesigns to accommodate the footprint of the new MEMs devices. The only options are to do a lifetime purchase of the product or to spend significant time and resources on redesigning and re-qualifying the electronics. In contrast to the MEMs vendors, many electrolytic tilt sensor companies have a more customer-centric approach to product and client support. They will make modifications to meet customer requirements and will sell at high or low volumes to meet customer demand. Tilt-sensor companies are committed to their products and their customers for the long term. Even while developing new, innovative components, they continue to produce parts from as far back as the 1960s, allowing customers to continue to produce legacy products without requiring frequently redesigns.
The Future of Electrolytic 傾斜感測器
For certain applications, MEMs tilt sensors are adequate in terms of cost, size, and performance. But for applications where drift and repeatability are of utmost importance or product lifetimes are measured in years, not months, electrolytic tilt sensors prove to be the superior product. Performance aside, certain electrolytics also offer a more attractive price point than comparably-performing MEMs devices. A metal dual-axis ±65° electrolytic sensor generally costs less than $5, whereas a MEMs device and electronics to provide similar performance can cost between $18 and $25, a difference of three-and-a-half to five times the price.
Innovations in electrolytic tilt sensor technology will further refine their performance and durability. Novel thick film-based glass tilt sensors will be able to measure with sub-arc second repeatability at significantly lower cost; ceramic sensors will be capable of operation at even higher temperatures; and new metal sensors will be able to combine high repeatability with larger measuring angles and smaller size. With recent and emerging innovations, coupled with the strong backing of their manufacturers, electrolytic tilt sensors will continue to be a proven, reliable, and cost-effective technology.